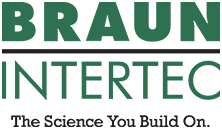
Stadiums. High rises. Major parking structures. On any given project, the Bloomington lab, which is also Braun Intertec’s HQ, will test thousands of concrete cylinders. That’s hundreds of tests every single day.
But, this high volume comes with increased complexity and costs:
- Purchasing and maintaining machines.
- Hiring, training and retaining technicians.
- Managing paper to record results.
It’s a lot of effort, and so much of it is manual and unscalable. In such an environment, testing accuracy, productivity and, as a result, costs are at risk.
THE CHALLENGE
Managing High-Volume Testing
Braun Intertec faced two major challenges in managing such a large-scale operation:
- 1. Keeping up with high-volume testing (and managing all the data)
- 2. Managing the curing room and cylinder disposal
Keeping Up With Testing & Managing Data
For Braun Intertec’s Concrete Lab Supervisor Ryan Kauffman, managing the sheer volume of cylinders was a major task. “My role is to oversee that all cylinders are tested properly and on time,” said Ryan. “In the past, on a good day, we could get results out by the end of the day. But usually, they would be ready by the next morning.”
And what did a day look like at Braun Intertec? Well, as the company grew in lockstep with the booming Minneapolis-Saint Paul Area, the lab tested upwards of twelve hours a day.
Technicians had to read hand-written labels to pull the right cylinder for testing. They loaded the cylinder into the machine and manually operated the full advance and metered advance valves until the concrete broke. Then, they manually wrote down every test result. This required technicians to physically flip through pages of break results (upwards of 40 pages in the summer; 15 in the winter). Once testing was complete, technicians brought the data to the project administrator to enter the data into Braun Intertec’s LIMS.
Finally, the data would go back to Ryan, who had to review and confirm that everything had been correctly recorded. It was an all-day process.
Not only did the lab staff have to keep up with long hours of testing, but they also had to make sure everything was accurate.
“When you’re testing 400-500 cylinders a day, mistakes in data can occur,” said Ryan. He referenced two primary sources of potential error that all concrete labs, large or small, have to recognize and correct.”
1. Inaccurate Break Strengths
“If a cylinder breaks in the machine at 8,350 psi, but someone types a three instead of an eight (i.e., 3,350 psi), you would have to investigate to see if that cylinder actually failed the test or not. If the reverse happens (the 3 becomes an 8), a sample would “pass” the strength test by mistake, when it should have failed.”
2. Incorrect Sample Number
“Let’s say you have a sample identified as #25873. But then accidentally write #25378. When all you do is look at numbers all day, by the end of it, all numbers look the same. Distractions come up. You forget to record one break. Data is lost.”
And, while it may sound minor, forgetting to record even one break could compromise an entire set of data.
Thor Stangebye, Braun Intertec’s Principal Materials Lab Manager, agreed. “We had a small error rate, but it doesn’t matter if we break 500 correctly. It’s the one cylinder you lose or break wrong that you have to investigate and correct.”
“It doesn’t matter if we break 500 correctly. It’s the one cylinder you lose or break wrong that you have to investigate and correct.”
Thor Stangebye, Principal Materials Lab Manager
The same principle held true when it came to managing the curing room.
Managing the Curing Room & Cylinder Disposal
The Bloomington lab’s curing room is the largest of Braun Intertec’s labs, storing about 10,000 cylinders at any given time.
Some of the most important specimens are the “hold” cylinders, which are held pending the results of the 28-day tests. If the 28-day test results are low or suspect, the hold cylinders are designated for testing at 56 days. If the 28-day tests are acceptable, the hold cylinders are discarded. This means that some cylinders are moved to a new location for testing at 56 days, and some are discarded.
But humans make mistakes. And sometimes they remove or throw out specimens from the curing room that they didn’t mean to. This means, concrete labs have to spend a lot of time and energy making sure these errors don’t happen. Because if one cylinder gets thrown out by mistake, the project engineer can’t verify that the concrete meets the right requirements. The only option is to send a team out to the job site to drill a core sample – an expensive endeavor. Concrete labs everywhere know that core samples are the last and least desirable resort, which is why Braun Intertec worked one step ahead by developing a spreadsheet system to keep track of all cylinders.
When technicians went to toss cylinders, they would have to look at a break list of previous results and compare to make sure they were tossing only the ones that had previously passed strength requirements. Then, Ryan would spend about thirty minutes a day managing the spreadsheet to make sure everything looked correct.
While this system worked, the solution was time-consuming, and it didn’t provide the peace of mind they needed. Braun Intertec wanted to find a way to secure the curing room and cylinder disposal process once and for all.
THE SOLUTION
Becoming a Truly Automated Lab
Braun Intertec needed a solution that could alleviate the challenges of high-volume, manual testing. As it turned out, they would only need one solution provider to solve both problems. And it was a team they knew well.
In 2014, Braun Intertec purchased one Forney’s new VFD Automatic Compression machines to reduce operator variance and improve testing consistency. The benefits of the VFD automatic were clear. So clear that by 2015, they had converted their two manual machines to automatic. And they added another VFD machine in early 2018 – bringing the total to four VFD automatic machines.
“Every technician operates manual machines a little different. But with Forney, it’s all automatic,” said Ryan. “We can replicate test results almost every time. If we test three cylinders at 28 days, the results are consistently within two percent of each other.”
But, despite the repeatability benefits of automatic, something was still missing.
Closing the Gap
Braun Intertec used its own software solution to capture data in the field and at the end of the construction materials testing workflow. The software worked well, but there was a gap in the middle.
Technicians would take wet concrete samples in the field and bring the samples back to the lab for curing and testing. But, at the machine, they still had to record test results on a clipboard. Then, someone would have to sit at a computer and type the results into their LIMS.
No matter how good the results were from automatic machines, they were still vulnerable to errors during this manual portion of the process. Not to mention the time it took for technicians to handoff data, administrators to type it all up and Ryan to verify everything.
Luckily, Forney had something else to offer to Braun Intertec’s Bloomington lab.
ForneyVault.
In 2018, Braun Intertec implemented ForneyVault, Forney’s new cloud-based integrated construction materials testing platform.
“There was a small learning curve, but I have to give it to Scott [Grumski, VP, Platform Development]. He was excellent in helping us,” said Ryan. “He flew out to our lab and personally got our machines running on ForneyVault.”
“Our volume is so high during the construction season, what we can do in 1-2 months, the average lab will do in an entire year,” Thor added. “So, we have unique circumstances that the Forney team has been ready to help with.”
Braun Intertec quickly learned that ForneyVault did much more than just fill the data management gap in the lab. The platform helped in two major ways:
- 1.Making automatic machines smarter
- 2. Creating an automatic curing room management system
Smarter Automatic Machines
Braun Intertec leverages ForneyVault and Forney VFD machines to the fullest extent. When cylinders are delivered to the lab, they are received via Braun Intertec’s LIMS, which sends the data to ForneyVault. Technicians can view and manage this data through ForneyVault’s interface, ForneyTools. From here, the technicians print labels with unique QR codes for the newly received cylinders and apply the labels to the cylinders as they strip them from their molds. Every cylinder is identified before being placed in the curing room.
With barcode scanners mounted on the side of the machine, technicians only have to pass the cylinder by the scanner before placing it in the testing chamber. This eliminates the need to read handwritten labels on cylinders—and eliminates the potential of misreading or breaking a cylinder on the wrong day.
This is because the QR code on the cylinder is connected to all previous sample data stored in ForneyVault. After scanning, the machine knows exactly what it is testing—and if that cylinder is supposed to be tested on that day.
The combination of VFD machines and ForneyVault created a highly productive process, where technicians could run on autopilot without missing anything important. In fact, one technician could now manage all four automatic machines.
Even so, that one technician still had “stand around time” while waiting for the cylinders to break. That’s why, in 2019, Braun Intertec purchased yet another VFD.
Braun Intertec arranged their five machines in a circle for maximum efficiency. With one technician, the workflow looked like this:
- 1. Pass the cylinder in front of the scanner and place into the testing chamber
- 2. Close the chamber door
- 3. Press start
- 4. Walk to the next machine to choose the break type of that machine’s previously tested cylinder
- 5. Clean up debris
- 6. Scan and place a new cylinder into this machine
- 7. Press start
- 8. Continue until there are cylinders testing in all five machines
- 9. By the time a test is started in the fifth machine, hear the break from the first machine
- 10. Pick the break type
- 11. Repeat the cycle
Before, technicians had to break cylinders at night so engineers could have results by the morning. Now, they can break them all during the day and have results to the engineers by the afternoon. There’s less stress on the technician and more focus on other important quality tasks.
“You have to be certified to break cylinders, but we don’t have to worry as much about training,” said Thor. “I don’t have to worry about slow testing, incorrect results, misreading cylinders or error proofing data.”
Automatic Curing Room Management
ForneyVault also eases the lab’s headaches related to managing the hold cylinders in the massive curing room.
“We were already using barcodes to scan cylinders right before testing. So, I asked Scott if he could develop a system that allowed us to scan cylinders and see if they were okay to toss – because they already made strength – or not – because they have not passed strength requirements,” explained Ryan. “When they gave us the system, Scott said, ‘Here it is. Let us know of any changes that will make it better.”
Fun Fact
Many of ForneyVault’s innovations grew out of working within Braun’s high productivity environment.
- Developed machine “smart checks” to allow technicians to work faster without missing basic errors like atypical diameter ratios, unrealistic dimensions or improper preload settings.
- Implemented notification features on the machines to provide important alerts, like low breaks, incorrect test dates or high variance.
- Developed Discard Dashboard to manage hold cylinders in the curing room.
DISCARD DASHBOARD:
How It Works
ForneyVault automates and verifies the “discard” management process.
Normally, technicians test cylinders at 7, 14 and 28 days. However, labs also keep some cylinders from that set on “hold” in the curing room, so they are able to be tested at later dates as needed.
In Braun Intertec’s case, they designate hold cylinders to be tested at 35 days. At this age, the cylinders are pulled from the curing room and scanned at the Discard Dashboard station. Based on the history of the sample, the cylinders are discarded or the test age is changed to 56 days. ForneyVault helps the lab decide what cylinders to keep or toss, keeping them compliant with ACI Standards. Plus, in ForneyVault’s cloud database, the full history of tests is available in an unalterable format forever, so the lab can always go back and verify strength.
STEP 1: Scan Cylinder at 35 Days
After scanning the cylinder, the full testing history of the sample (all previous breaks) will populate.
STEP 2: View Results
Instead of having to look at a break list of previous results and manually decide if the cylinder passed strength requirements or not, Discard Dashboard automatically provides results through an easy-to-understand color system.
For example, for concrete with an expected strength of 5,000 psi:
GREEN: SAFE TO DISCARD
This means the average of the three 28-day tests is above 5,000 psi, and there’s not one individual specimen that is less than 4,500 psi.
YELLOW: OKAY TO DISCARD, REQUIRES CONFIRMATION
If the average of those three tests is above 5,000 psi, but one of the specimens was lower than 5,000 (but not lower than 4,500), ACI Standards say that the concrete is okay. A yellow alert essentially tells the technician that there was one 28-day cylinder that broke low, but it’s probably okay because it’s not over 500 psi lower. However, it’s up to the lab to decide if they are comfortable with these results enough to discard.
ACI Standards also call for an average of three 28-day results for 4” x 8” cylinders, or two results for 6” x 12” cylinders. If there are 28-day results that meet strength requirements, but there are not the proper number of cylinders tested, the scanned cylinder will be presented in yellow. If the technician attempts to discard this cylinder, Discard Dashboard will require additional verification before allowing the discard.
RED: HOLD THE CYLINDER
If the average of those three tests is less than 5,000 psi and/or any individual specimen is less than 4,500 psi, ACI Standards say that the concrete has not met expected strength. So, Discard Dashboard will alert the technician to keep the cylinder. The technician will have to change the age to break to 56 days, reprint the label and set it in the curing room until day 56 to see if it meets the right strength at that time. There are multiple steps required to discard this cylinder, preventing accidental discard.
“We haven’t lost a single cylinder since implementing Discard Dashboard,” said Ryan. “We noticed results pretty immediately because, when we first started, I ran Discard Dashboard in parallel with my spreadsheet system. But after a week of use, I saw it was working and stopped using my spreadsheet. This saves me 30 minutes a day, but it’s really about the mental knowledge that I don’t have to worry about tossing the wrong cylinders. That peace of mind is worth way more than those 30 minutes.”
THE RESULTS:
Productivity, Quality & Much More
“In my world, quality and productivity is key. We’ve nailed it with the system. It’s given us both.”
Ryan Kauffman, Concrete Lab Supervisor, Braun Intertec Bloomington, MN
The productivity gains easily made up for and justified the initial investment of automatic machines and ForneyVault. But the benefits don’t stop there. The combination of automatic machines and ForneyVault’s powerful integration capabilities has all but eliminated the variance of manual processes and the hard work of mitigating any potential errors. This means higher quality and security. More time saved. Less risk. Less costs.
From the Bloomington lab team themselves, here are the benefits they have uncovered:
Productivity
As the Greater Minneapolis-Saint Paul Area grew, so did Braun Intertec’s business. By 2018, they were seeing numbers of samples coming in like never before. “We were really struggling to keep up. We were always operating at 100-125%,” said Ryan. “Within 3 months of implementing ForneyVault, not only were we keeping up but we also were above the water. Now, we can spend more time on each individual sample quality, not doing the busy work.”
Quality & Security
If a project engineer questioned results, Ryan can go into ForneyVault and see the full history of tests, including who tested the cylinder at what time, what the rate ramp was – everything. Before, this data was handwritten. Thus, questionable. And the data available did not include the original X-Y graph of stress vs. time – now it does, forever.
“Now, I can prove it,” said Ryan. “And when our project engineers ask us if we’re sure the results are right, I can honestly say they are 100% correct with absolute certainty.”
Time Saved
In the concrete world, the testing timeline doesn’t stop for a holiday. After implementing ForneyVault, the Christmas Eve shift, for example, was much more manageable.
Ryan said: “I tested around 200 cylinders, reviewed data and reported it all in just three hours. Before ForneyVault, that would have been a full 8-hour workday. From a production standpoint, you can’t beat it.”
Competitive Advantage
At a higher level, Braun Intertec’s ability to handle more volume with more accuracy unlocks their potential to win more testing contracts.
“We do not worry if we get a large project like we used to. Before, we’d accept large projects but might have to hire someone else to help, adding to our costs. Now, we can handle anything.”
Thor Stangebye, Principal Materials Lab Manager
A Lifelong Partnership Based on Innovation
The Bloomington lab’s success is largely due to the strong partnership between the Braun and Forney team. “Forney is really good to work with,” said Thor. “They don’t just sell us stuff. They work with us.”
“I know there’s someone on the other end of the line,” added Ryan. “I can call and someone will answer for me.”
But their success also speaks to Braun Intertec’s innovative nature. The problems from manual testing processes are widespread in the concrete industry, and, without ForneyVault, Braun Intertec spent a lot of time and manpower making sure errors didn’t happen. But then, they were innovative enough to take advantage of ForneyVault early on. This only led to even more innovation in the lab.